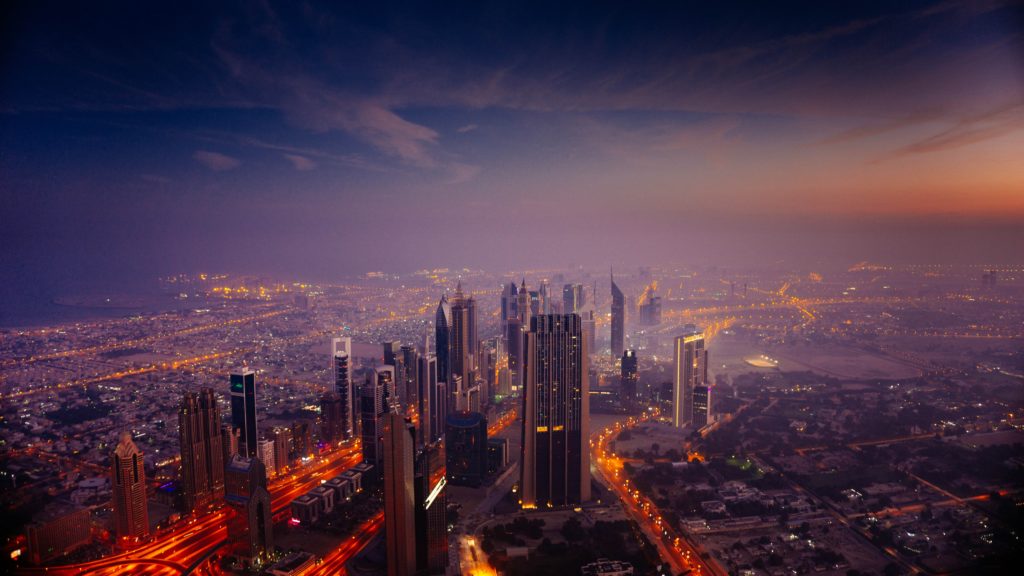
The concept of Industry 4.0
The aim of this series of blog is to provide a high-level view of the threat landscape of a smart factory as well as the potential attack vector used to infiltrate such a smart factory. The first part will be a definition of Industry 4.0 and its components (Smart Factories, IoT, and CPS). The second part will focus on the issues around industrial cybersecurity and the potential risks of non-resilience of the plants of tomorrow in the light of existing technologies. Real-life examples will be provided as well.
History of Industry 4.0
The term Industry 4.0 was first publicly introduced in 2011 as “Industrie 4.0” by a group of representatives from different fields (such as business, politics, and academia) under an initiative to enhance the German competitiveness in the manufacturing industry.
The German federal government adopted the idea in its High-Tech Strategy for 2020. Subsequently, a Working Group was formed to further advise on the implementation of Industry 4.0.
Promises of Industry 4.0
The concept of industry 4.0 or industry of the future corresponds to a new way of organizing the means of production. This new industry is emerging as the convergence of the virtual world, digital design, management (operations, finance, and marketing) with the products and objects of the real world. The big promises of this concept are to seduce consumers with unique and personalized products, and despite low manufacturing volumes, to maintain a profit. These same consumers can thus communicate with the machines during the production phases: this type of production is called « smart production ». According to this principle, in the context of industrial automation, this is characterized by the implementation of sensors which are the basic elements of data acquisition and control systems (SCADA). They make it possible to transform physical quantities (temperature, pressure, position, concentration, others …) into signals, most often electrical, which give information on these quantities. These sensors allow the robots of a production line to dialogue and adapt the production tool to different needs, in a non-exhaustive way, the maintenance, the needs of the markets or the modifications of the customers.
In addition to the technological aspects, Industry 4.0 affects different aspects of our modern societies. New challenges emerge through this new way of producing. Industry 4.0 obviously affects the economic aspect but also has social, political or environmental impacts. It raises the question of the employment of millions of employees around the world. Indeed, the support of current employees and the training of future employees must be taken into account. This means that machines will operate independently or cooperate with humans in creating a customer-oriented production field that constantly works on maintaining itself. The machine rather becomes an independent entity that is able to collect data, analyze it, and advise upon it.
This becomes possible by introducing self-optimization, self-cognition, and self-customization into the industry. The manufacturers will be able to communicate with computers rather than operate them.
It is still unclear for many scientists and historians if the concept of Industry 4.0 is part of the Third industrial revolution or on the contrary if it belongs to the fourth. It is not the goal of this paper to answer this question, rather we will be focusing on defining the core principle of Industry 4.0 and the benefits it will bring to the current factories. While the first waves industrial revolution focused on improving return on investment (in terms of money, manpower, or energy) of the production, it has become clear that each of these revolutions had a long-lasting impact on the daily life of millions, if not billions, of people. The concept of Industry 4.0 is no exception.
Cyber-Physical Systems, Internet of Things, and Smart Factory are the most common three terms cited in academic research publications related to the industry. Consequently, and given its initial stage, these are the three main components of the industry 4.0.
Smart Factories
Smart Factories are a key feature of Industry 4.0. A smart factory is a system that is able to deal with both the physical world as well as the virtual. It is aware of the surrounding environment such as the state of the demands, the global economy, the stock of the different components that composed the product it is building, etc. A Smart Factory can be defined as a factory where CPS communicate over the IoT and assist people and machines in the execution of their tasks.
It is important to note that a single smart factory is not a suitable system. As of today, there is no single end product that is produced in just one factory. In order to fully embrace the Industry 4.0 concept, all the factories needed to produce one product should be communicating with each other through a Cyber System responsible for collecting data from each smart factory and cordoning the different actions based on both internal and external factors. Each of these smart factories could be in different cities or countries, and the communications would be made using the internet. Moreover, employees need to have visibility over what is happening in every factory and need to be able to operate them at a distance. The industry 4.0 concept also hold the promise of true zero stock factories, meaning that a good will be only produced if there is a demand for it and it won’t stay in the warehouse for long, therefore it is important that every action of a customer is recorded and integrated in the Cyber-system for better decision management
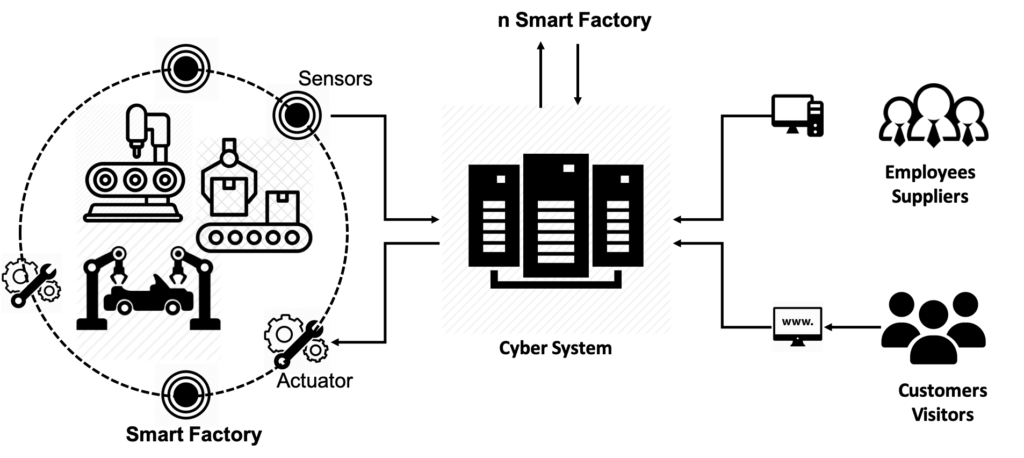
Cyber-Physical System (C.P.S)
A Cyber-Physical System can be defined as a system where a digital element collaborates together in order to command, control and provide visibility over physical elements. The CPS of a Smart Factory would be comprised of:
- Sensors that collect data and send it to a datacenter – cyber-system;
- Actuators that are responsible for achieving order received by a datacenter;
- The cyber-system which is responsible to receive data from actuators, process it, and send order and tasks to the actuator.
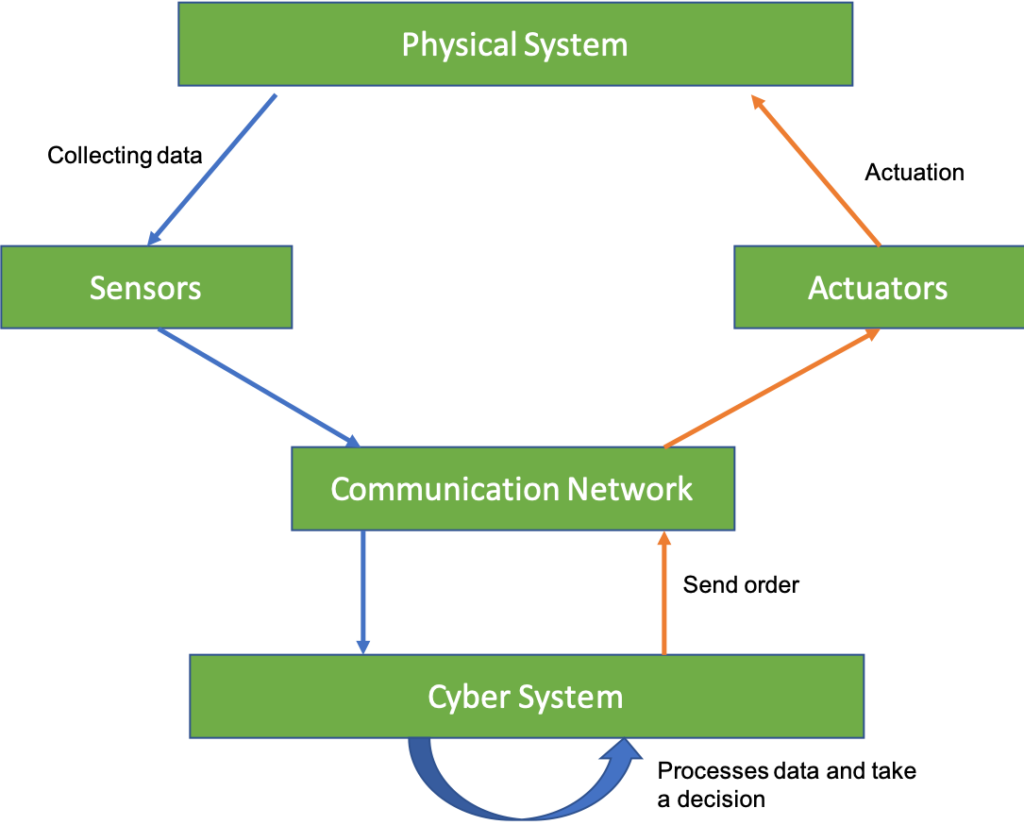
The Internet of Things
It is not uncommon to see sensors and actuators referred to as IoT objects. These sensors or actuators usually communicate over the Internet either directly via WIFI or 4G or through a gateway with which they communicate using radiofrequency such as the LoRa Network. In this case, the gateway is responsible for collecting the message from all the sensors, sending it to the CS, and dispatching the messages received from the cyber-system to the different IoT objects.
In the world of smart factories, it is recommended for sensors and actuators to communicate through a gateway as it allows for more scalability and resilience for the CPS model. In fact, when using a gateway, the cyber-system is only required to keep a connection open whereas if every sensor and actuator communicate directly with the cyber system, the cyber-system has to keep as many open connections as there are sensor and actuator which lead to high consumption of CPU and less stable system. The most used protocols to communicate between the Gateway and the CS are HTTP and MQTT over a secure TCP connection.
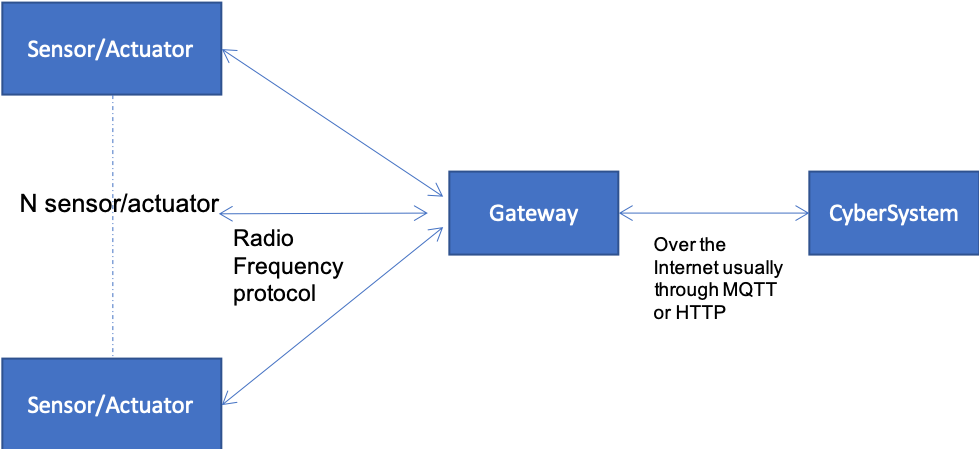